Quantensprung
Mit "Digital Sealing" setzt die Audi-Lackiererei im ungarischen Győr jetzt ein neues, automatisiertes Verfahren zur Karosserieabdichtung ein. Die neue Methode ermöglicht es, Dicke und Breite des Materialauftrags frei zu bestimmen. Dadurch gelangt das Dichtmaterial millimetergenau und schneller als bisher auf die Oberfläche.

Ein robotergeführter Applikator trägt ultrafeine Tropfen präzise und in gleichbleibender Qualität auf die Karosserie auf. Die optimale Breite und Dicke des Materialauftrags programmieren geschulte Anlagenfahrer vorab. Dank dieser Präzision wird so gut wie kein Abdichtmaterial verschwendet. Bonus: Durch den reduzierten Materialeinsatz lässt sich das Gesamtgewicht des Autos um mehrere Kilogramm verringern – und damit sowohl die Fahrdynamik verbessern als auch die CO2-Emissionen verringern. Auch die Mitarbeiter profitieren: Ihre Arbeit wird künftig in ergonomischer Hinsicht deutlich leichter. Vor allem an schwer zugänglichen Stellen, an denen zugleich hohe Qualitätsanforderungen an die Dichtigkeit gelten, bringt das neue Verfahren Vorteile. Bisher erforderten diese Arbeitsschritte oftmals viel Erfahrung und die Arbeitsbedingungen waren belastend – bis hin zu Überkopf-Arbeiten am Unterboden des Fahrzeugs.
Verbesserte Ergebnisse bei hohem Einsparpotenzial
Gido Hoppe, zuständig für Product Engineering Lackierte Oberfläche / Korrosionsschutz bei Audi und „Digital Sealing“-Projektleiter, erinnert sich an eine Diskussion zur Konstruktion des Fahrzeugs: „Es ist sehr unschön, wenn man die PVC-Raupen durch die Spalte der Heckklappe sehen kann. Wir haben uns hier auf die Suche nach einer neuen, besseren Lösung gemacht. Die Gründe für die Entwicklung des „Digital Sealing“ lassen sich wie folgt zusammenfassen:
- Weder Höhe noch Breite der PVC-Naht ließen sich bisher frei bestimmen
- Muss man beim Applizieren die Auftragsrichtung ändern, ist kein durchgängiger, konstanter Auftrag möglich
- Hohe Verschmutzung der Applikationskabinen (Overspray)
- Ergonomieverbesserung für die Mitarbeiter
- Höhere Präzision und bessere Schichtdickenkontrolle
Audi-Experte Hoppe betont die Vorteile, die sich heute ergeben: „Wir erreichen Material- und damit Gewichtseinsparungen im zweistelligen Prozentbereich. Zwar muss jedes Fahrzeug individuell und im Einklang mit der Qualitätskontrolle betrachtet werden. Aber der Materialverbrauch kann bis zu 50% geringer ausfallen, die manuelle Nacharbeit ebenfalls um bis zu 40%.“ Hinzu komme ein verbessertes Erscheinungsbild der PVC-Raupe. Hoppe weiter: „Wir benötigen keine Schablonen, um präzise Kanten zu erzielen, und es kommt zu keinerlei Overspray während des Auftrags.“ Das automatisierte Abdichtverfahren kann bei der Grob- und Feinnahtversiegelung sowie bei einer zukünftig geplanten Unterbodenbeschichtung zum Einsatz kommen, wobei die Dimensionen der PVC-Raupe sich frei wählen lassen. Es werden sehr geringe Volumenstromraten verarbeitet und manuelle Prozesse reduzieren sich oder können teilweise ganz entfallen. Letzteres spart Produktionszeit.
Dichten wie gedruckt
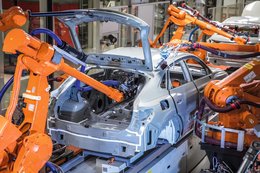
Dichten wie gedruckt kann man mit dem Applikationsverfahren „IDDA.Seal“. Auch komplexe Geometrien lassen sich präzise und effektiv abdichten.
Das zugehörige Verfahren „IDDA – Intelligent Dynamic Drop Application“ – wurde von Atlas Copco Industrial Assembly Solutions entwickelt. Im Gegensatz zum konventionellen Auftrag, bei dem ein beständiger Volumenstrom fließt, kommt es nun zu einem Tropfen-Auftrag in hoher Frequenz. „Von Punkten zur Linie und von Linien zur Oberfläche“, so beschreibt Dr. Sten Mittag, Research & Technology Manager bei Atlas Copco, die Methode. So könne jedes Tröpfchen etwa hinsichtlich des Volumens individuell manipuliert werden. Mittag erklärt: „Wir erreichen ein signifikant größeres Auftragsfenster, bei einem Abstand zwischen Applikator und Bauteil von 3 bis 80 mm und einem Auftragswinkel zwischen -25° und +25°. Die Auftragsgeschwindigkeit reicht von 50 bis 600 mm/s. Die Schichtdickensteuerung erfolgt durchgängig zwischen 0,3 und 2 mm.“ Mittag, seitens Atlas Copco Projektverantwortlicher, weist zusätzlich auf die Flexibilität hin: „Es entsteht eine äußerst präzise Naht mit individuellem Querschnitt.“
Next steps
Aktuell setzt Audi das Verfahren „IDDA.Seal“ – so die Bezeichnung der Applikationstechnologie für Abdichtungen in Lackierstraßen – in der Feinnahtabdichtung des Q3 und Q3 Sportback im ungarischen Győr ein. Hier beträgt die Nahtbreite zwischen 8 und 11 mm. Erste Serienanwendung war dabei das Abdichten der Ausschnitte für die Rückleuchten, der so genannten Leuchtentöpfe. Um die Mitarbeiter entsprechend zu schulen, entstand in einer Try-Out-Zelle ein Nachbau des Roboters aus der Linie. So sind produktionsunabhängige Versuche möglich. Von ersten Tests im Januar 2019 kam es im August zum Umbau der Linie sowie zum Serienstart. Bis einschließlich November wurden bisher mehr als 40.000 Fahrzeuge entsprechend bearbeitet. Gido Hoppe blickt freudig in die Audi-Zukunft: „Bald soll auch die Applikation von Grobnähten folgen. Wir sprechen dann von Nahtbreiten zwischen 15 und 18 mm. Hierfür wird dann lediglich das Applikator-Modul gewechselt, die Anzahl der Düsen bleibt gleich.“ Dies soll im August 2020 abgeschlossen sein. „Neben einer verbesserten Ergonomie, höher Prozesssicherheit und mehr Nachhaltigkeit können wir dann noch mehr Nacharbeit reduzieren, die Umwelt schonen und erhalten viel höhere Freiheitsgrade bei der Karosserie-Gestaltung“, fasst er zusammen. Das Verfahren ist bereits zum Patent angemeldet und soll zukünftig an weiteren Standorten ebenso zum Einsatz kommen.
Zum Netzwerken:
Audi AG, Ingolstadt, Gido Hoppe, Tel. +49 841 890, gido.hoppe@audi.de, www.audi.com
Atlas Copco Industrial Assembly Solutions GmbH, Bretten, Dr. Sten Mittag, Tel. +49 7252 5560-4115, sten.mittag@atlascopco.com, www.atlascopco.com/de-de
Hersteller zu diesem Thema
Dann brauchen Sie mehr als aktuelle Internet-News - Sie brauchen die Fachzeitung BESSER LACKIEREN! Exklusive Interviews, Analysen und Berichte. Praxisbezogener Fachjournalismus. Umfassende Informationen. Digital oder gedruckt - So, wie Sie es brauchen.